In addition to metallurgical elements, water chemistry has a powerful affect on the corrosion process in zirconium alloys. The management of water chemistry as required in numerous reactor methods include appropriate additions of lithium hydroxide, boric acid, hydrogen/deuterium, oxygen, iron, and zinc. In PWRs, boric acid is added to the coolant water for reactivity management. The pH of the coolant is adjusted by addition of lithium hydroxide which renders the coolant barely alkaline, so as to scale back the corrosion rates of structural materials (stainless steels and Inconels) within the primary heat transport circuit and thereby inhibit deposition of corrosion merchandise on the gasoline cladding. Radiolysis of water produces oxidizing species which boosts oxidation price of zirconium alloys within the radiation surroundings .
The fireplace rose 20 storeys in just 35 minutes to engulf the total peak of the tower on 14 June 2017. The inquiry has heard professional evidence that the flames spread by way of the cladding system and had been fuelled by the extremely flamable panels. Chartered engineer Dr Jonathan Evans was a part of the group testing cladding for the government after the Grenfell Tower hearth. because of their corrosion resistance to acids and bases and their low neutron-absorption rates.
Standard Zry is sufficiently onerous to be prone to stress-corrosion cracking (SCC) when the pellet–cladding hole closes and the swelling gas generates substantial tensile hoop stresses in the cladding. In the presence of an aggressive fission product (iodine is most frequently cited), a brittle crack may be initiated and penetrate the cladding wall. This is a main cladding failure that admits steam into the rod with the accompanying potential for a extra severe secondary failure due to hydriding. The combination of conditions (vulnerable metallic, tensile stress, and chemical enhancer) that produces the primary defect is termed pellet–cladding interplay (PCI). The original function of tin in Zry was to mitigate the lack of corrosion resistance attributable to pickup of impurity nitrogen throughout fabrication of the alloy.
The government’s building safety programme has focused totally on instant interim mitigation actions and everlasting alternative of unsafe aluminium composite material (ACM) panels on high-rise buildings due to the acute risks posed by such panels.
The unfold of the fire up the outside wall, if any, was then monitored. The Independent Expert Advisory Panel additionally suggested the department to ascertain a research venture to test and improve the evidence obtainable on the behaviour of a variety of non-ACM supplies used in cladding techniques when subjected to fireside.
Grenfell cladding firm: 'fire could have been put out learn the facts here now with simple extinguisher'

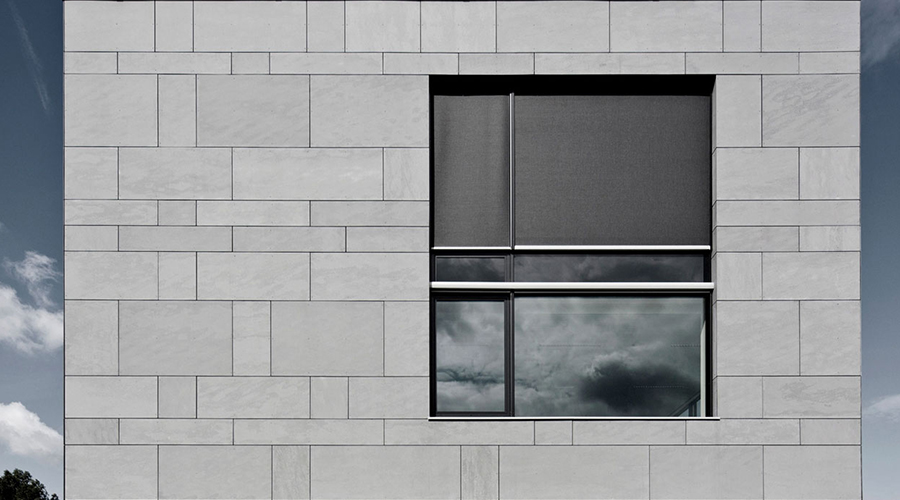
Most of the metallic cladding for the constructing trade is pre-painted in coil prior to the manufacturing of the cladding panels. Metal cladding is used for each protection from environmental elements and aesthetics of the constructing. The paint applied by coil coating offers the steel more durability, corrosion resistance and final appearance. Arconic argued that the tragedy at Grenfell was not the results of its panels, however the combination of materials used in the 2016 £10m refurbishment, singling out the plastic window frames via which the fire was believed to have first spread from flat sixteen into the cladding system.
Phase transformation of Zirconia is, nevertheless, of great concern. Zircaloys additionally endure from bad creep charges. In contrast to surface-layer welding, explosive welding causes no change in microstructure, and corrosion resistance of the layers isn't affected (Pocalco 1987 ). ions from the environment to the response front on the steel/oxide boundary.
Due to the combined results of thermal expansion of gas pellets, gasoline swelling because of fission gas launch, and the coolant stress on the outer floor of fuel tubes, cladding tubes collapse on the fuel pellets. In PWRs the closure of the hole between the pellet and the clad takes about one full power 12 months whereas the gap is maintained for a longer period in BWRs.
The interplay that gasoline cladding tubes experience as a result of fission products on the inner surface is stress corrosion cracking (SCC). Iodine, caesium, and cadmium are some of the fission products which contribute strongly to the SCC course of.
Metal is the most energy-efficient and sustainable constructing supplies available. Next to this it's nearly completely recyclable and current steel coils contain a excessive recycling content as much as 95%. The engineering of our supplies also makes our cladding a powerful resilient form of exterior overlaying . The bonding agent reinforces the picket components, and our additives improve the cladding’s weather resistance.
Cladding is an outer layer of both vertical or horizontal material, used to improve the appearance, thermal insulation and the climate resistance of a constructing. Our cladding is available in quite a lot of sizes, kinds of timber and surface finishes. Enhance the curb attraction of your own home with B&Q cladding. All of our timber is responsibly sourced forest pleasant timber. Once the pellet/clad hole is closed, any change in pellet dimensions causes stress in the cladding and the synergy between the stress and the corroding medium induces the SCC course of.
Zry is available in two varieties, Zry-2 and Zry-4. These two differ by minor changes in the concentrations of the transition metals (Zry-4 has no nickel). PWRs use Zry-4 whereas BWRs employ Zry-2 as cladding and both Zry-2 or Zry-4 for the duct or channel holding the gas-factor bundle. The transition metals iron and chromium appear in the microstructure as precipitates of the intermetallic compounds Zr 2 (Ni,Fe) and Zr(Cr,Fe) 2 . These minor alloying parts improve corrosion resistance to an extent dependent on the dimensions of the precipitates.
As a treatment, speedy cooling of the Zry ingot throughout fabrication (referred to as beta quenching) produces a much finer intermetallic precipitate inhabitants. This distribution of the transition metals maintains the strength of the Zry however improves its corrosion resistance, possibly by brief-circuiting charge-transport paths between the scale surface and the metallic–oxide interface. In order to remove waterside corrosion of cladding as a life-limiting process, modified Zircaloys have been developed. Under PWR water circumstances, decreasing the tin content of Zry to 1% and adding a comparable concentration of niobium produces an alloy with a corrosion fee several instances decrease than that of the standard Zry.
The joint is then attributable to a deformation-induced melting bathtub. The soften layer is quite skinny; for example, when cladding an aluminum alloy it is about 0.5–fourμm (Kreye 1985, 1997 ). The dilution of the molten zones leads to airplane or corrugated interfaces.
The oxidation course of and the character of the oxide layer on a zirconium alloy sample are schematically illustrated in Fig. 6 .
With the event of an equilibrium pore and crack structure in the oxide layer, the oxidation rate successfully becomes linear, a attribute characteristic of the post-transition oxidation behavior. Alloying components, particularly tin, niobium, and iron, current in the α-stable answer strongly influence each the kinetics and the mechanism of oxide growth in zirconium alloys. The thickness of the cladding is a design parameter dictated by conflicting efficiency requirements.
EN clad volume_up try this website adjective
During mechanical decladding, the gasoline assemblies are chopped and the gas core is leached with nitric acid, leaving behind the undissolved cladding materials for disposal as a solid waste. This methodology is adopted for zircaloy-clad fuels from power reactors and chrome steel-clad fast reactor fuels. Cladding tools is generally designed to swimsuit a specific product or a bunch of products; this particularly applies to the items required for uncoiling of the strip and the feeding device. The material and floor of the rolls as well as their geometrical form (cylindrical or crowned) are essential. Depending on the supplies to be bonded, cleaning and roughening are best accomplished by brushing, grinding, or scraping using a specifically designed cutter with needles.
The interplay that fuel cladding tubes expertise because of the fission merchandise on the internal floor is stress corrosion cracking (SCC). Iodine, caesium, and cadmium are a number of the fission products which contribute strongly to the SCC course of.
In order to prevent or reduce pellet/clad interactions, each mechanical and chemical, a coating of graphite powder is applied on the internal floor of cladding tubes. The graphite layer provides lubrication to attenuate the mechanical interactions, and acts as a barrier towards the migration of harmful species to stressed regions of fuel tubes. Laser cladding usually includes masking a relatively inexpensive substrate materials with a dearer alloy that may improve the resistance of the half to wear or corrosion. Cladding permits the bulk of the part to be made with inexpensive materials, whereas offering the floor with desirable properties related to the more expensive cladding materials.
The helium filling gas is also a fairly good conductor, however solely so long as it remains uncontaminated by fission merchandise. The poorly conducting ceramic fuel pellets are responsible for the majority of the temperature rise. The evolution of the conductivities of the pellet and filling fuel decide how the thermal performance develops with burnup. As the oxide layer grows, the compressive stress on the outer layer of oxide isn't sustained and consequently the tetragonal section becomes unstable and transforms into the monoclinic phase. Such a transformation causes the formation of a fine interconnected porosity in the oxide film which allows the oxidizing water to come back involved with the steel floor.
The effect of lack of steel by internal or outer corrosion is less important for thick cladding than for skinny-walled tubing. For the same external loading, the stress produced within the cladding, both exterior from the coolant or inside from fission-product swelling of the fuel, is lowered in proportion to the wall thickness. However, thick cladding is detrimental to neutron economy, increases the quantity of the reactor core, raises fuel temperature, and costs more than thin-walled tubing. The compromise between these competing calls for has produced wall thicknesses of ∼0.9mm in BWRs and ∼0.7mm in PWRs. is produced and the risk of a large secondary hydriding failure is increased.

2.7 click this link Zr-Based Alloys


The buildup of those may be suppressed by adding hydrogen in the coolant water. Dissolved hydrogen concentration in PWR coolant is maintained at a degree of two.2–4.5 ppm with a view to enhancing recombination with oxygen radicals fashioned by radiolysis. The PHWR coolant does not contain boric acid and deuterium is added instead of hydrogen. Dissolved oxygen in PHWR coolant is controlled between 10–50 ppb and it has been noticed that corrosion in each zircaloy-2 and Zr-2.5 Nb pressure tubes rises to an exceptionally excessive worth at excessive oxygen concentrations.
In addition to metallurgical factors, water chemistry has a robust influence on the corrosion course of in zirconium alloys. The management of water chemistry as required in several reactor methods embrace suitable additions of lithium hydroxide, boric acid, hydrogen/deuterium, oxygen, iron, and zinc. In PWRs, boric acid is added to the coolant water for reactivity management. The pH of the coolant is adjusted by addition of lithium hydroxide which renders the coolant slightly alkaline, so as to scale back the corrosion rates of structural materials (stainless steels and Inconels) in the main heat transport circuit and thereby inhibit deposition of corrosion products on the fuel cladding. Radiolysis of water produces oxidizing species which boosts oxidation rate of zirconium alloys within the radiation surroundings .
Differential swelling between cladding, wrapper tube, and spacing system (spacer wire or grids) can induce extra stresses and deformations on these parts and/or generate coolant move perturbations in the bundle. These phenomena have been studied and have notably proven that wires or grid supplies have to be chosen and specified so as to minimize differential swelling. Laser cladding has been utilized to hardening of steam generator turbine blades and reached pilot production standing [four ].
Phase transformation of Zirconia is, nevertheless, of nice concern. Zircaloys additionally undergo from unhealthy creep rates. In contrast to floor-layer welding, explosive welding causes no change in microstructure, and corrosion resistance of the layers is not affected (Pocalco 1987 ). ions from the surroundings to the response entrance at the metallic/oxide boundary.
These frameworks have been applied and peer reviewed throughout the scope of fireside research research on the fireplace performance of aluminium composite panels and insulation materials at The University of Queensland and the University of Edinburgh. This massive scale check, undertaken by the Fire Protection Association (FPA), tested a HPL panel system with stone wool insulation, in accordance with British Standard 8414. This take a look at includes building a 9-metre excessive wall with a complete cladding system fastened to it - together with panels and insulation. This was then subjected to a hearth designed to duplicate the circumstances in which a severe hearth breaks out of a window.
The fire rose 20 storeys in just 35 minutes to engulf the total top of the tower on 14 June 2017. The inquiry has heard expert evidence that the flames spread by way of the cladding system and had been fuelled by the extremely flamable panels. Chartered engineer Dr Jonathan Evans was a part of the group testing cladding for the federal government after the Grenfell Tower hearth. due to their corrosion resistance to acids and bases and their low neutron-absorption charges.
The joint is then caused by a deformation-induced melting bathtub. The soften layer is kind of thin; for instance, when cladding an aluminum alloy it is about 0.5–4μm (Kreye 1985, 1997 ). The dilution of the molten zones leads to aircraft or corrugated interfaces.
The unfold of the hearth up the skin wall, if any, was then monitored. The Independent Expert Advisory Panel additionally advised the division to determine a research project to check and enhance the evidence obtainable on the behaviour of a range of non-ACM supplies used in cladding techniques when subjected to fireplace.
Standard Zry is sufficiently onerous to be prone to emphasize-corrosion cracking (SCC) when the pellet–cladding hole closes and the swelling gas generates substantial tensile hoop stresses in the cladding. In the presence of an aggressive fission product (iodine is most frequently cited), a brittle crack may be initiated and penetrate the cladding wall. This is a major cladding failure that admits steam into the rod with the accompanying potential for a extra critical secondary failure as a result of hydriding. The mixture of circumstances (susceptible metal, tensile stress, and chemical enhancer) that produces the primary defect is termed pellet–cladding interplay (PCI). The original function of tin in Zry was to mitigate the lack of corrosion resistance brought on by pickup of impurity nitrogen throughout fabrication of the alloy.
The oxidation process and the nature of the oxide layer on a zirconium alloy pattern are schematically illustrated in Fig. 6 .
Zry manufacturing methods now offer far better control of gaseous impurities than early fabrication know-how, so the original reason for including tin is moot. Since tin is a substitutional impurity, its function is to increase the strength of Zry over that of pure zirconium.
The blades had a machined pocket, into which powdered cobalt-based metal (Stellite 6) was fed forward of the laser beam. The resulting cladding layer was well bonded, and the blades exhibited improved fatigue characteristics in contrast with blades formed by the traditional silver brazing process.